切削加工ねじ VS. 冷間圧造ねじ
現在流通しているねじは主に「切削(切削加工)」と「圧造(塑性加工 鍛造とも呼ばれます)」の2種類の方法によって作られています。それぞれの特徴について簡単に解説します。
「ねじ」の製造方法って?
身近に存在する「ねじ」。「産業の塩」とも呼ばれスマホを始め、ありとあらゆるものに使われる、私たちの生活に不可欠な縁の下の力持ちです。
この「ねじ」ですが、どうやって作られるか意識されたこと、ありますか?「そんなこと考えたこともない」あるいは「旋盤で削りだすんじゃないの?」「溶かした金属を型に流し込むのでは?(いわゆる鋳造)」と想像する方は多いと思います。想像力たくましい方は「頭の部分とねじの部分を別々に作ってくっつける」と思われたかもしれません。恥ずかしながら私はこの業界に入るまで考えたことがありませんでした。皆さんはどのようにして作られると想像されましたか?
現在流通しているねじは主に「切削(切削加工)」と「圧造(塑性加工 鍛造とも呼ばれます)」の2種類の方法によって作られています。
切削加工
「切削加工」は木材から像を作り出す彫刻のイメージと言えば伝わるでしょうか?

ねじの場合は、材料となる棒材や線材から旋盤(加工したい素材を回転させ、刃物をあてることにより、円筒形状に削り出す機械)やNC旋盤(数値制御(Numerical Control)の機能をもたせた旋盤)、あるいは専用のねじ切旋盤により文字通り削り出します。

この「旋盤による切削加工」を行えるようになって初めて、私たちはねじを機械で量産できるようになりました。ねじ・ボルトを製造する初めての機械は1568年にフランスのベッソンによって作られた、という記録があります。
冷間圧造
「圧造(塑性加工)」は「鍛造」とも呼ばれる金属加工技術の一種です。粘土に力を加えて形作る陶芸のようと言うとイメージが伝わるでしょうか?粘土のように金属も力を加えて塑性変形(ある一定以上の力を加えて変形させると、変形したままもとの形に戻らなくなること)させることができます。もっとも粘土と金属では変形させるのに必要な力のスケールが桁違いですが。
ねじ全体を機械で圧造することは、切削加工と比較すると新しい製造方法です。圧造によるねじ製造の原型が登場するのは、大きな圧力を生み出すことができる機械装置が誕生する18世紀半ばから19世紀にかけて起こった産業革命の頃まで待つ必要がありました。
この圧造によるねじの成型過程は大きくねじ頭部を成型する「ヘッダー」とねじ山を成型する「ローリング」の工程に分けることができます。最初の工程はねじ頭部を成型する「ヘッダー」加工です。コイル状に束ねられていた材料を引き延ばして真直ぐにした棒材や線材を決められた寸法にカットし、ダイス(固定側)とパンチ(移動側)で挟み込むようにして加圧してねじ頭部を成型します。これらは「ヘッダー(クランク機構によって駆動される横型プレスの一種 ちなみに上から圧力をかける加工を「鍛造」、横向きに圧力をかける加工を「圧造」と呼び分けることがあります)」と呼ばれる機械によって行われます。

変形させる度合いが大きいと何段階かに分けて圧力を加えます。変形の割合が大きいほど多段階になり、2パンチ×3ダイスまでの機械を「ヘッダー」、4パンチ×4ダイス以上の機械は「ホーマー」と呼び分けることもあります。この工程でできるねじ山のないねじは「ブランク」と呼びます。
ブランクは転造工程「ローリング」へ送られます。ねじ転造ダイス(丸ダイス式・平ダイス式・プラネタリ(ロータリー)式の3タイプがあります)で「ブランク」を挟み込み回転させながら圧力をかけることで、ねじの山部はブランクの径より盛り上がり谷の部分は元の径より凹んでねじ山が成型されます。
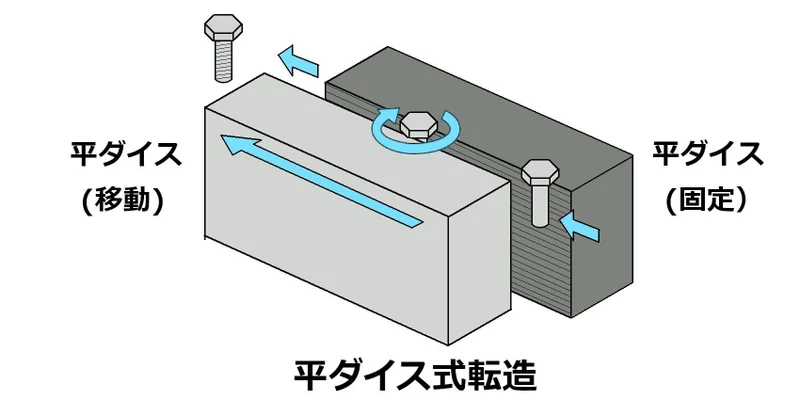


圧造によるねじ加工は加工温度により「冷間圧造」「温間圧造」「熱間圧造」と区別されます。常温のもとでの加工を「冷間圧造」と呼びます。大きなサイズは塑性変形し易くするために再結晶温度以上に熱して加工する「熱間圧造」によって加工します。2つの中間の温度の加工が「温間圧造」です。これら3つの内「冷間圧造」は熱による素材への影響がなく機械的特性や仕上がりが大変優れています。
「ねじ」は製造技術の進歩により、精度の高いものが大量に生産されています。現代では「ねじ」は重要な部品ながら「産業の塩」と呼ばれるほどに気軽に使える、安価でありふれた存在になりました。

「切削加工」と「冷間圧造」の二つの方法の特徴を比べると、「冷間圧造」は原材料の節約、二次加工の排除など多くの点で優れています。勿論「切削加工」にも優れた点があるので、製品の品質を向上させつつ利益を最大化する最適なねじを選択するためにも、その特徴を知ることは有益です。では、それぞれの特徴を少し見てみましょう。
「切削加工」VS.「冷間圧造」 強度
「切削加工」と「冷間圧造」によるねじの最も重要な違いの1つは“強度”です。冷間成形部品は、切削加工部品よりも強度があります。なぜでしょうか?理由を以下に挙げます。
加工硬化
冷間成形中に金属が移動し、打たれるたびに硬さや引張強さが増します。これを加工硬化と呼びます。これにより低炭素鋼・アルミニウム・真鍮などの柔らかい材料が、成型加工の一工程ごとに強度を増します。また一部のグレードのステンレス鋼については、いかなる熱処理にも反応せず冷間圧造された場合にのみ硬くなります。そのため冷間圧造でこうしたステンレス鋼製のねじを製作すると、切削加工品よりもはるかに高い強度になります。
優れた材料
冷間圧造に使用される材料は、圧造用に特別に設計されています。なぜなら冷間圧造でなされる加工は鋼線材にとっては過酷でかつ材料の表面がそのまま製品の仕上がり面となるので、「強靱で割れない、折れない」「均質で不純物が少なくて加工性が良い」「傷がなく寸法精度および表面の良好なこと」が要求されるからです。このため冷間圧造用の材料(専用に調整されたSWCH規格の鉄材)は通常、切削加工用よりも優れたグレードの材料として分類されます。この事は製品の質を高めます。
途切れのない “ファイバーフローライン”
鋼材にも木材に見られる木目や繊維方向のような金属組織の流れが存在し、「ファイバーフローライン」と呼ばれます。これはメタルフローラインや鍛流線と呼ばれることもあります。冷間圧造されたねじのファイバーフローラインは切断されずにパーツの形状に合わせて圧縮されるため、結果的に靭性や耐摩耗性を向上させます。

応力集中が少ない
冷間成形により線材の金属はダイスに沿って移動します。加工の際に生じる大きな力はダイスとパンチの寿命を短くするので、工具の金型設計上には角Rの仕上がりに一部制限があります。そのことが首下の半径を大きくし、結果的に首下の応力集中によるストレスを軽減してねじの耐久性を高めます。

「切削加工」VS.「冷間圧造」 コスト
冷間成形部品は、切削加工部品よりも次の理由でコスト削減が期待できます。
材料の歩留まりが極小
材料の歩留まりの差は注目に値します。圧造加工のスクラップは平均1〜3%ですが、ねじ切削加工では75%ものスクラップが発生する可能性があります。スクラップはリサイクルできてもその際に排出されるCO₂のことを考えると、冷間圧造は地球環境にやさしい加工法ともいえるでしょう。
高速加工
冷間圧造は切削加工に比べ製造速度が非常に速くなります。冷間圧造の製造速度は驚くほど早く、まさに瞬く間にねじを成型します。しかも冷間圧造品は寸法精度も高く切削加工で生じるようなバリが発生せず、ねじ面は非常に滑らかな鏡面表面仕上げになります。

複雑な形状へ対応
複数の部品を組み合わせるアセンブリを単一の冷間成形部品に変換できるなら、複雑な形状のねじ部品を切削加工するよりも低コストで製作できます。現在では予備成型を複数回行える多段ヘッター、特に4パンチ×4ダイス以上の「ホーマー」と呼ばれる機械の登場により、驚くほど複雑な形のねじ部品を冷間圧造で製作できるようになっています。
また冷間圧造技術を使用し、完成形または完成形に近い形状の部品へ簡単な追加工をすることでもコストを削減できます。例えば、複数のねじ加工部品を一緒にプレスして一体化することや2つ以上の圧造品を溶接することです。これらの追加工により、切削加工と比べて大幅な加工時間の短縮やコスト削減を実現しながら高い強度を持つねじを製作できる場合があります。
切削加工が有利な場合
ただし、すべての部品が冷間圧造に適しているわけではありません。例えば試作品です。たとえ数個を試作するだけであっても、冷間圧造で製造するにはヘッダー用のダイスやパンチ、転造ダイス等の金型が必要です。金型製作のためには多くの時間と費用がかかるので、少量の試作なら金型を必要としない切削加工が圧倒的に有利です。

次のようなねじ部品は切削加工が適しています。
• ヘッドとシャンク(軸)の比率が小さい、または無い
• リセス(+穴や六角穴のようなねじの駆動溝)がない
• 全長が短い
• 複数の異なる直径から成る(場合による)
• 低コストの材料を使用する
• 必要量が少ない(小ロット生産)

ねじの製造方法それぞれの利点を理解することは、優れたねじ部品を用いつつコスト削減の機会を捉えるための第一歩です。
ねじの製造・選定について詳しくお知りになりたい方はボサードまでお問い合わせください。