現代のモノづくりのためのワイヤーねじインサート
モノづくりの世界で締結部品(ファスナー)は、組み立てられたコンポーネントの完全性と耐久性を確保する上で重要な役割を果たします。ねじ締結の場合、ねじの損傷、摩耗、ねじ山の破損などの問題が大きな課題となります。この点でワイヤーねじインサートは、信頼性の高い効果的なねじ山補強のソリューションを提供します。
ワイヤーねじインサートはボルト接合部のねじ山の破損の修復用品として広く知られています。ホームセンターやECサイトで、ねじ穴補修・再生用品としてインサート本体に下穴用ドリル、専用タップと挿入工具等がセットになったものがねじ穴補修キットとして販売されています。こうした補修用の商品は、お気に入りの製品を長く使用するためのとても便利なツールです。

モノづくりの分野において、ワイヤーねじインサートの主な役割は、木材、プラスチック、複合サンドイッチパネル、アルミニウムなどの柔らかい素材に対して、ねじ穴を強化することです。この役割により、ワイヤーねじインサートは、現代の製造業の軽量化・省資源化に応える複合材、プラスチック素材、3D プリントの使用といった課題解決に貢献します。
ワイヤーねじインサートとは?
ワイヤーねじインサートは、菱形の断面を持つ精密に設計されたワイヤーコイルです。


あらかじめ開けた下穴(下穴径はメーカーの指定を必ず守ります)に専用工具にてタップ・本体挿入をしてねじ山を成形・補強します。
挿入前のワイヤーねじインサートは、挿入前の自由外径(外力の加わらない開放されている状態)が母材のねじ穴よりも15~20%ほど大きく、軽く絞り込まれながら挿入されます。

挿入されたインサートは弾性により自由外径に戻ろう(広がろう)とし、母材にしっかり固定されます。
通常のねじの場合、おねじとめねじのリードの誤差や角度の誤差により、接触率は60%以下とされています。

そのため、噛合うおねじに対する荷重比率は、ねじ頭側の第1山に約50%、第2山に25%、第3山に13%と不均一な応力分布となります。これは、ボルト・ねじの破断が第1山から第3山で生じやすい理由でもあります。
ワイヤーねじインサートは、おねじとめねじのねじ山のピッチと角度の誤差を補正します。そのため、ねじの接触率は90%になり、各ねじ山に対する荷重比率も理想に近い均等な応力分布となります。こうして疲労によるねじ山の破断を防ぎ、応力の集中を減らし、締結強度を高めます。

この特性は、耐久性のあるねじ接合が必要な場合や、かじりやすい柔らかい金属製品の場合に特に有効です。また、他のタイプのねじインサートに比べて軽量・コンパクトであることも現代のモノづくりの軽量化・小型化の要求に一致しています。

ワイヤーねじインサートは、挿入工具の先端溝へ引っ掛ける折り返しのある「タング付き」と、引っ掛け溝を加工して折り返しをなくした「タングレス」に大きく分けることができます。「タングレス」では、タングの折り取り作業が省け、挿入方向も指定がありません。最近は、タングが付いていても装着後に折り取る必要のない製品も登場しています。
また、コイルの中央部分を多角形状にしてねじの緩み止め機能のある製品もあります。ロックタイプはタング付き・無しどちらにも用意されています。

ワイヤーねじインサートは通常、SUS304(18-8)鋼線を菱形の断面に圧延して作られていますが、インコネル・ナイモニック90・ナイモニック60・リン青銅・SUS316などの材料の製品もあります。また、カラーワイヤーねじインサートは、挿入忘れのような加工時のヒューマンエラーを防ぎます。

ワイヤーねじインサートは、メートル並目と細目、ユニファイ並目と細目(UNC / UNF)、さらには英国規格(BSW・BSC・BA・BSP)、アメリカ規格(NPT)など様々な規格に対応した製品があり、サイズも2mm~100mmと幅広くカバーしていて、航空宇宙産業・自動車・電子機器・通信機器・医療機器・船舶などの幅広い分野で活用されています。
現代のモノづくりとワイヤーねじインサート
3Dプリント製造とワイヤーインサート
3Dプリンタは高速試作だけでなく、出力したものをそのまま最終製品として使用する「ダイレクト製造」や、従来の製造工程の中に3Dプリンタを取り入れて効率やコストを下げることを目指す「インダイレクト製造」等で、モノづくりの現場で注目されています。
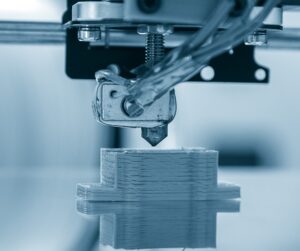
一般的に3D プリンタにて製造された部品には、組立前にサポート材の除去、研磨や平滑化、塗装やコーティングなどの仕上げといった、後処理が必要です。
加えて、強固なねじ接合が必要な箇所では、ねじ穴の補強が必要になります。成形後に挿入できるワイヤーねじインサートは、この必要を満たすのにぴったりのソリューションです。インサートを挿入することで、高精度に設計されたねじ山が得られ、ねじ穴の耐久性が向上し、組み立てと分解の繰り返しが可能になります。ただし、非常に頻繁に組立・分解を繰り返さなければならないのであれば、重量は増えますが一体型のインサートの使用を検討してください。

参考:3Dプリンタ 原理と特徴
3Dプリンタにはさまざまなタイプがあり、それぞれ異なる原理で動作し、使用できる材料も異なります。現在よく知られているタイプの3Dプリンタについて少しだけ触れます。
現在の主流は熱溶解積層方式(FDM Fused Deposition Modeling)です。このタイプのプリンタは、プラスチックフィラメントを加熱して溶かし、ソフトクリーム製造機のようにノズルからフィラメントを押し出して、一筆書きで1層1層積み重ねます。溶けたプラスチックが冷えて固まることで、オブジェクトが形成されます。そのため材料押出法(Material Extrusion)とも呼ばれます。射出成形で用いられるプラスチック材料そのもので出力するので、最終製品に近い物性のリアルで機能的な試験が可能です。短所は層の積層跡が目立ち、仕上がりの精度がやや劣ることです。また、金属の成形はできません。
光造形方式(SLA Stereolithography)はもっとも古い3Dプリンタの方式です。液体状の光硬化性樹脂(レジン)のプールに、レーザーや紫外線を照射して硬化させて層を形成します。レジンが光に反応して固まり、オブジェクトが形成されます。プロジェクターによって面一括露光でレーザーよりも早く硬化させるプリンタ(DLP方式)も実用化されています。長所は高精度で滑らかな表面仕上げが可能で複雑な形状も再現できることです。短所は材料費が高く、太陽光などにより劣化しやすいこと、洗浄やサポート材の除去といった後処理が必要であることが挙げられます。
粉末焼結方式(SLS Selective Laser Sintering)は、レーザーで粉末材料を焼結(部分的に溶かして結合)させて層を形成します。この方式の長所は、高強度で耐久性のある部品を作成できること、また、サポート材が不要で複雑な形状も簡単に作成可能であることです。逆に短所は、プリンタ自体が高価で、粉末材料の取り扱いが難しいことです。
そして金属粉末をレーザーで焼結(溶融)させて層を形成するものはDMLS(Direct Metal Laser Sintering)と呼ばれます。レーザーを複数本搭載し、アルゴリズムを工夫することで、表面に継ぎ目ができないシームレスな造形を可能にしたプリンタもあります。この方式の長所は高精度で強度の高い滑らかな金属部品を作成できることです。特に航空宇宙や医療分野で利用されています。利用分野から想像できるようにプリンタおよび材料費が非常に高価であり、安全対策や粉末の取り扱いが難しいことが短所と言えます。
インクジェット方式は、馴染みのあるプリンタの印刷方式を応用したもので、インクジェットヘッドから噴射した樹脂を紫外線で固めながら積層して作成していきます。マテリアルジェッティングと呼ばれることもあります。印刷のように高解像度なカラーで造形を作成することができ、表面の仕上げも滑らかで非常に高精度な作品に仕上がります。短所はアクリル系樹脂を使用しているため耐久性が弱く、直射日光が当たると劣化することです。
粉末固着方式(バインダージェッティング)は、ヘッドから光硬化性樹脂を結合材として噴射し、敷き詰められた石膏や樹脂パウダーなどの粉末材料を固めていく方式です。長所は粉末材料に着色することで、きめ細かいフルカラー造形が出来ることです。造型スピードも早く、材料費は安く抑えられますが、同時に耐久性が低く、石膏を固めたものは衝撃に弱く、壊れやすいというデメリットがあります。
複合サンドイッチパネルとワイヤーインサート
複合サンドイッチパネルとは、ハニカム構造体や発泡体、バルサ材やグラスウールといった心材を2枚の面板で挟み接着して一体化したパネルです。表材とコアを様々に組み合わせること軽量で高強度に加えて、耐熱性や断熱、衝撃吸収性や美観等の多様な性能を実現できるため、航空宇宙産業をはじめ、建築、輸送、海洋、風力発電等、様々な分野で利用されています。

サンドイッチパネルは、面内方向(パネル面と平行な方向)の外力には表板が、面外方向(パネル面と垂直方向)の外力にはコア材が受け持つことで、軽量でありながら曲げ剛性を大きくできるという特徴があります。
表面板にはアルミ合金板やFRP板が用いられるのが一般的です。心材には、アルミ合金やFRP製のハニカム構造体、発泡プラスチックなど(発泡コア)、あるいはグラスウールなどが用いられます。
一方、複合サンドイッチパネルはボルトやねじを用いての締結・固定が難しい材料です。しかしながら、このサンドイッチパネルにワイヤーねじインサーを適用することにより、ねじ接合用の強固な取り付けポイントを作成することができます。パネルコアの適切な位置に固体ブロック材料を配置すると、複合ハニカムパネルや発泡コアパネルにドリル穴を開け、ワイヤーインサートを組み込むことができます。
ねじ締結のための別のソリューションとしては、ブラインドリベットナットやbigHead®のようなボンディングファスナー、また、超音波と摩擦により急速にコネクションを作成できるMM-Welding® (マルチマテリアル ウエルディング)テクノロジーを利用する等が考えられます。



参考: ハニカムコア(honeycomb core)
蜂の巣のような六角柱のセルをすき間なく並べたものがハニカムコアです。六角形は、すき間なく平面を埋めることができる3つの正多角形(正三角形、正方形、正六角形)のうち、同一周長で面積を最大にする図形です。つまり、材料を最も効率よく利用できる構造体と言えます。

ハニカムコアの一般的な素材は、アルミニウム、ポリプロピレン、厚紙などです。ハニカムコアは単体ではなく、ハニカムコアを芯材として六角柱のコアをふさぐように上下の表面板が硬く結合したサンドイッチ構造として使用されます。ハニカムサンドイッチ構造にすることにより、軽量化とともに曲げにも強い構造となります。
ハニカムコアパネルは、パネルに加わる曲げる力をハニカムの六角柱の壁の伸縮応力に変えることで変形をより小さくしています。ジュースの空き缶を想像していただくとわかりやすいかもしれません。空き缶(円柱)の側面を握ると簡単につぶすことができますが、缶を上下方向で押しつぶすことは大変です。同様にハニカムコアも上下方向の圧縮(伸縮)にはたいへん強く、パネルを曲げようとする力 -ハニカムコアにはとっては面外方向の力- が加わると、ハニカムコアはこの力に対抗して、結果としてパネルの曲げ変形を抑えます。また、ハニカムコアの苦手な面内方向の応力に対しては、上下の表面板が対抗し面内方向の剛性も改善されるのです。
発泡コア(Foam Core)
発泡材は、製造時に気体を含有させた、細かい孔が多数空いている多孔質体です。発泡材の生成には、溶解したガスから気泡を発生させたり、発泡剤の熱分解を利用したり等の様々な方法があります。発泡成形品は、非常に軽く強度もあり、パネルを効果的に軽量化します。発泡心材としてよく知られているのは、発泡ポリスチレン、発泡ポリプリピレン、発泡ポリウレタンなどです。

大量生産に適しています
ワイヤーねじ込みインサートには、生産環境での組み立てを高速化し、精度を高めるパワーツールが用意されているものもあります。こうしたツールは、手持ち操作用に構成することも、モジュールや自動化システムのアッセンブリツールとして組み込むこともできます。
航空宇宙産業でささやかに始まったねじ込みインサートは進化を遂げており、その実用性はねじ穴の修理における評判をはるかに上回っています。この魅力的なファスナー、ワイヤーねじインサートを利用したいとお考えですか?どうぞボサードへご相談ください。